For Amazon sellers using non-DDP (Delivery Duty Unpaid) ocean shipping, managing customs clearance and taxes can feel overwhelming. Unlike DDP (Delivery Duty Paid) services, non-DDP shifts compliance responsibilities to the seller, requiring meticulous preparation and knowledge of international trade rules. This guide breaks down the process into actionable steps, helping you avoid delays, fines, and unexpected costs while ensuring smooth delivery to FBA warehouses.Step 1: Document PreparationSuccessful customs clearance starts with accurate paperwork. Essential documents include:A commercial invoice detailing product descriptions, prices, and Incoterms (e.g., FOB).A packing list specifying box weights, dimensions, and contents.A bill of lading issued by the shipping carrier.Product-specific certifications (e.g., FDA for food or FCC for electronics).Verified HS codes (6–10 digits) to determine duty rates.In the U.S., submit an Importer Security Filing (ISF) 24 hours before shipment loading. Missing or incorrect documents can trigger customs holds or fines.Step 2: Duty and Tax CalculationsTax liabilities depend on two components:Customs duties: Calculated as (product value + shipping + insurance) × duty rate (based on HS codes). For example, plastic goods (HS 3926.90) face a 3.4% U.S. duty rate.Additional fees:In the U.S., pay a 0.3464% Merchandise Processing Fee (MPF).In Europe, Value-Added Tax (VAT) ranges from 15% to 27% of the CIF (cost, insurance, freight) value.Always verify duty rates using official customs databases before shipping.Step 3: Risk Mitigation StrategiesAvoid common pitfalls:HS code disputes: Provide product composition details or manufacturing processes to support classifications. Request a binding ruling from customs (e.g., CBP Ruling in the U.S.) for high-value goods.Undervaluation audits: Declare at least 65–70% of the Amazon listing price. Customs may use platform prices to reassess undervalued shipments.Port delays: Schedule trucking and FBA appointments early. Most ports allow 5 free days for container pickup before charging demurrage fees (e.g., $150/day in Los Angeles).Step 4: Cost-Saving OpportunitiesOptimize expenses with these methods:Duty exemptions: Leverage trade agreements like USMCA for goods produced in Mexico or Canada.VAT deferral: In Europe, delay VAT payments by registering a local tax number.Bulk filings: Consolidate multiple shipments into one customs entry to reduce processing fees (e.g., U.S. MPF drops to $27.75 per filing).Step 5: Post-Clearance LogisticsAfter customs approval:Arrange drayage to Amazon warehouses within the free demurrage period.Secure FBA delivery appointments via Seller Central, especially during peak seasons.Verify FNSKU labels to prevent warehouse rejections. Mislabeled items incur $50+ remediation fees.FAQsHow long does customs clearance take?Simple declarations take 1–3 days. Complex items or inspections may extend this to 5–10 days.What if duties are overcharged?File an appeal within 90 days (use CBP Form 19 in the U.S.).How to handle rejected shipments?Choose between re-exporting (costly) or local destruction (requires environmental permits). Purchase abandonment insurance beforehand.ConclusionNon-DDP shipping offers cost savings but demands attention to detail. Start with small shipments and consider hybrid solutions like “customs-cleared non-DDP” services, where agents handle paperwork while you pay actual taxes. For high-volume sellers, transitioning to DDP can streamline operations as sales grow.Pro Tip: Regularly review customs updates and collaborate with China freight forwarders and local brokers who specialize in Amazon-bound cargo. By mastering these steps, you’ll minimize risks, reduce costs, and build a resilient supply chain for global expansion – from factory floors in Shenzhen to FBA warehouses worldwide.
2025-03-03
5
Amazon FBA
Freight Rate
Overseas Warehouses
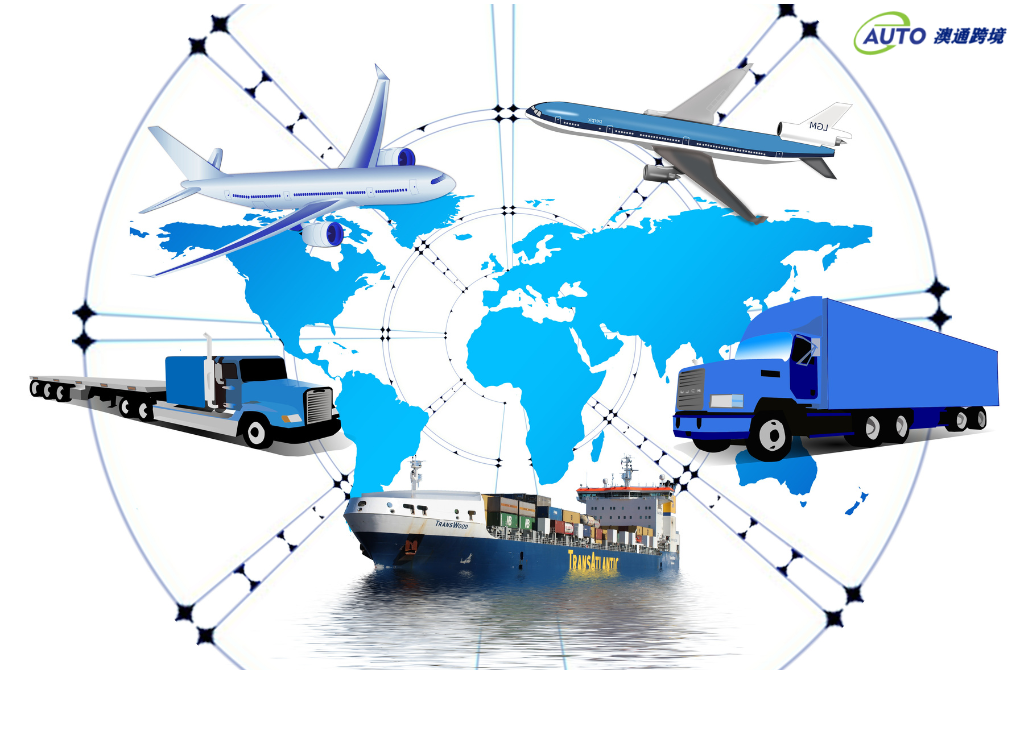
Operating a business that depends on international shipping is a challenge and costly. But here's the good news: utilizing US international warehouse transit can dramatically reduce the cost of logistics. If you're an online retailer or managing inventory across different sales channels, here's how a good warehouse can cut costs across all levels.Lowering Peak Season Shipping CostsThe holidays can be a nightmare for logistical experts. Shipping costs rise when demand increases, and traditional methods usually fail to meet the needs. If you ship your goods to a US overseas warehouse before the peak season, you will save yourself the cost of shipping charges.Ship in the off-season to keep from high shipping costsDistribute shipments over time to lessen the effect of sudden demand surgesBenefit from lower freight rates when shipping costs for global shipping are lowerReducing Storage FeesSuppose you're just beginning to learn about the game or do not have sufficient storage space in your home. In that case, warehouses in overseas transit services let you store goods in huge quantities without worrying about the cost of storage over the long term.Keep your storage costs down by transferring goods only when requiredMake use of the free storage times that some warehouses provideAvoid the risk of accumulating overstocked inventory in your warehouse at homeOptimizing Multi-Platform OperationsFor businesses that sell on multiple platforms, such as Amazon, eBay, and others, US overseas warehouses are the ideal solution to reduce the cost of storage and shipping.Effectively distribute products across different platformsSave money on warehouse charges by consolidating inventory into one locationImprove delivery times for customers from multiple marketplacesReducing Stockouts and Missed SalesNothing is more frustrating than running out of stocks. Warehouses in overseas locations allow you to efficiently replenish your stock without the usual delays associated with international shipping. You'll be stocked and keep your sales going.Beware of missed sales opportunities that are due to out-of-stock itemsMore rapid restocking results in more sales during periods of high demandStop listings from being removed from visibility or being penalized for not being in stockSimplifying Returns and ExchangesReturns can become a major logistical headache, especially when dealing with international shipments. The presence of a US warehouse for the management of returns makes the process easier, reducing shipping costs and freeing you from stress.Handle returns locally instead of paying international return feesRefunds and exchanges are processed faster to improve customer satisfactionSave money on international return shipping costs by handling your return directly through the USReducing Risks and Improving EfficiencyWhen you ship products internationally, there's always a chance of risk. However, having a US international warehouse may help minimize the risk of product returns, repackaging, or even non-compliance issues.Make use of relabeling and repackaging services to get your products back on track fastReduce the possibility of damage to your product or theft in shippingReduce shipping delays and costs caused by regulatory or customs issuesAccessing Discounted Shipping RatesUS overseas warehouses typically collaborate with local carriers and often receive higher rates than independent businesses. This means they can access lower shipping rates, which can further reduce the overall cost of logistics.Get the benefit of local warehouse agreements with major carriers like UPS, FedEx, and USPSBenefit from bulk shipping rates to save money on delivery optionsTransfer the savings to your customers, or keep the differenceFAQsHow do US overseas warehouses aid me in reducing costs during the busy season of the holidays?By storing your items in a US overseas warehouse prior to peak season, you will save on high shipping costs. Additionally, you can divide your deliveries to ensure that costs are reasonable and on time.What are the typical costs for using the US overseas warehouse?Fees vary by the level of service and warehouse; however, you'll generally be charged storage costs, which are determined by the size and amount of items stored. Additional fees could include shipping, order processing, and return handling.How can I manage my returns with a US overseas warehouse?Yes. The US overseas warehouse could assist you in managing local returns, reducing the shipping charges for international returns, and expediting refunds or exchanges.What is the procedure if my product requires packaging or labeling repackaging?Many US overseas warehouses offer repackaging or relabeling services to ensure that your products conform to local requirements. This reduces the possibility of fines or shipping delays.How can US overseas warehouses help me save money on shipping costs?Warehouses usually have agreements with local transport companies, which give you discounts on shipping costs. This can dramatically reduce the cost of shipping compared to handling your shipments independently.ConclusionIf you're looking to cut costs and increase the efficiency of your logistics, using the US shipping service to overseas warehouses is a great alternative. From avoiding peak-season shipping surges to reducing costs for storage and improving return handling, these options offer many advantages. Keep your logistics easy, quick, and cost-effective by utilizing the full benefit of US overseas warehouse services today.
2025-02-14
8
Overseas Warehouses
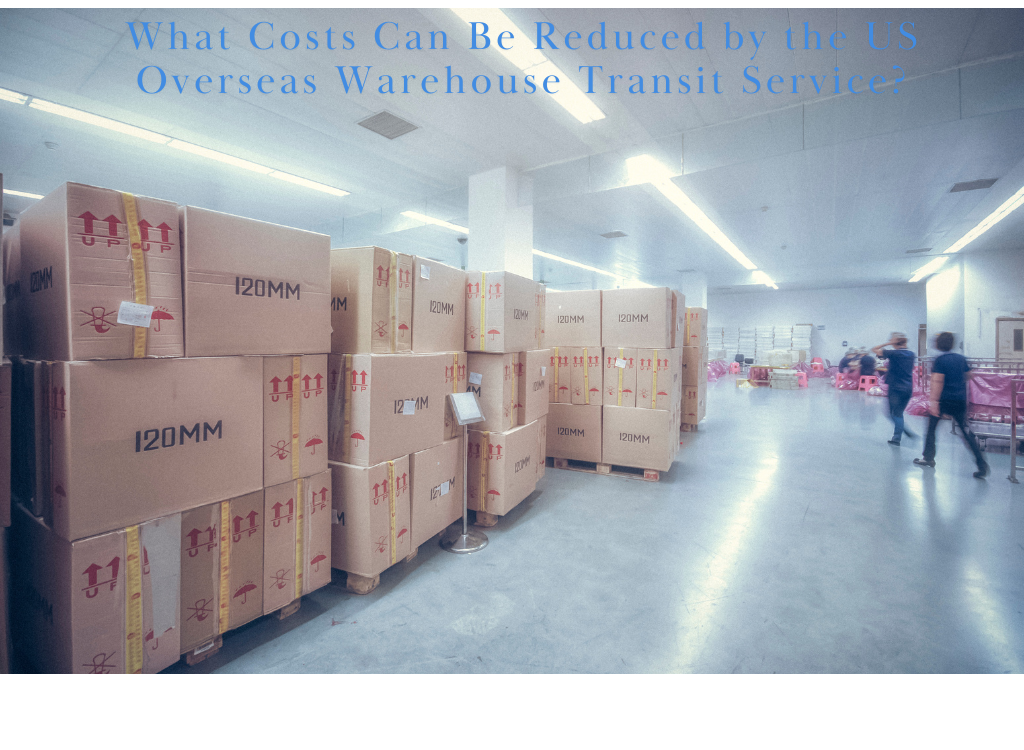
Navigating Amazon's Fulfillment by Amazon (FBA) system can be a game-changer for your e-commerce business. However, ensuring your products are correctly labeled is crucial for smooth operations. In FBA, product labels (FNSKU labels) and shipment labels serve distinct purposes. Understanding the differences between these labels can help you avoid costly mistakes and streamline your logistics process. Here's a comprehensive guide to help you distinguish between product labels and shipment labels in FBA.Understanding the Two Types of LabelsTo effectively manage your inventory and shipments within Amazon's FBA system, it's essential to grasp the fundamental differences between product and shipment labels. Both labels play pivotal roles, but they serve unique functions that cater to different aspects of the fulfillment process. To understand their specific purposes and applications, let's delve deeper into each type.Product Labels (FNSKU Labels)FNSKU stands for Fulfillment Network Stock Keeping Unit. These labels are unique identifiers Amazon assigns to each product you sell through FBA.Identification: FNSKU labels are unique to each product, allowing Amazon to track inventory accurately. They typically start with prefixes like "XOO" or "B0" and overlay the product's original barcode.Application: Each product unit must have an FNSKU label attached to its packaging. This ensures that Amazon can identify and manage each item separately within its vast fulfillment network.Purpose: The primary role of FNSKU labels is to enable Amazon's system to recognize and track your inventory. This ensures that products are correctly stored, picked, and shipped to customers, maintaining the integrity of your stock.Shipment LabelsShipment labels differ from product labels and are used to manage the overall shipment sent to Amazon's warehouses.Outer Package Identification: Shipment labels are affixed to the exterior of the boxes you send to Amazon. These labels include a shipment ID (e.g., FBAXXXXXX) and a shipment number.Multiple Box Identification: If your shipment consists of multiple boxes, each box will have a unique identifier like U001, U002, etc. This helps Amazon distinguish between different boxes within the same shipment.Purpose: Shipment labels facilitate the efficient handling of your packages upon arrival at Amazon's fulfillment centers. They help warehouse staff quickly verify which shipment the boxes belong to and ensure accurate processing and storage.Key Differences Between Product Labels and Shipment LabelsUnderstanding the distinct roles of product and shipment labels is crucial for maintaining an organized and efficient FBA process. Here are the primary differences that set them apart:Usage ContextProduct Labels: These are used for individual product identification within Amazon's inventory system. Each product unit in your shipment must have its own FNSKU label.Shipment Labels: Used for managing entire shipments and their constituent boxes. These labels are only applied once per box, regardless of the number of products inside.Application ProcessProduct Labels: You must print and apply an FNSKU label to every product unit. This requires careful attention to ensure each item is correctly labeled before shipping.Shipment Labels: Print a shipment label for each box in your shipment. The number of shipment labels corresponds to the number of boxes you send to Amazon.Visual IdentificationProduct Labels: Typically smaller and placed directly on the product's packaging, covering the original barcode. They contain the FNSKU code, which is unique to each product.Shipment Labels: Larger and placed on the outside of the shipping boxes. They include shipment IDs and box numbers, making them easily visible for quick identification.Practical Scenarios: When to Use Each LabelTo ensure your shipments are processed smoothly, knowing when and how to use each type of label effectively is important. Here are some common scenarios:Single Product ShipmentIf you're sending a shipment containing only one type of product, each unit will have an FNSKU label, and each box will have a shipment label. This ensures that both individual products and the overall shipment are properly tracked.Multiple Product ShipmentEach product unit will still require an FNSKU label for shipments containing different types of products. Additionally, each box will need a shipment label with a unique box number to differentiate between the various products inside.Printing and Applying LabelsCorrectly printing and applying labels is crucial to avoid errors during fulfillment. Here's how to handle each type of label:Printing Product LabelsQuantity: Print one FNSKU label for each product unit in your shipment.Quality: Use a high-quality printer to ensure the barcode is clear and scannable. Blurry or smudged labels can lead to scanning errors and inventory issues.Placement: Place the FNSKU label outside the product's packaging, covering the original barcode if necessary. Ensure it's easily accessible for scanning.Printing Shipment LabelsQuantity: Print one shipment label for each box in your shipment.Visibility: Attach the shipment label to a flat surface outside the box. Avoid placing labels on seams or corners where they might be obscured.Durability: Use durable label paper to withstand handling and transportation without tearing or fading.Best Practices for Labeling in FBAImplementing best practices for labeling can significantly enhance the efficiency and accuracy of your FBA operations. Here are some recommendations:Double-Check Requirements: Always refer to Amazon's latest FBA labeling guidelines to ensure compliance. Requirements may change, and staying updated helps avoid mistakes.Organize Your Shipment: Clearly label each box and product to streamline the receiving process at Amazon's warehouses. Organized shipments reduce the risk of errors and delays.Use Labeling Software: Consider using specialized FBA labeling software to automate the process, especially for larger shipments. This can save time and minimize human error.Test Scannability: Before finalizing your shipment, test the scannability of your labels to ensure Amazon's systems can read them without issues.Keep Backup Labels: Have spare labels on hand in case of printing errors or damaged labels. This ensures you can quickly replace any problematic labels without disrupting your shipment timeline.ConclusionCorrectly distinguishing and applying product labels (FNSKU) and shipment labels is essential for a seamless FBA experience. By understanding their differences and following best practices, you can ensure your products are accurately tracked and efficiently processed within Amazon's fulfillment network. Proper labeling prevents inventory errors and enhances your overall logistics efficiency, contributing to better customer satisfaction and business growth.For more detailed information, always refer to Amazon's FBA Labeling Guidelines and stay updated with any policy changes to maintain compliance and optimize your FBA operations.
2025-01-06
4
Amazon FBA
Overseas Warehouses
Sea Freight
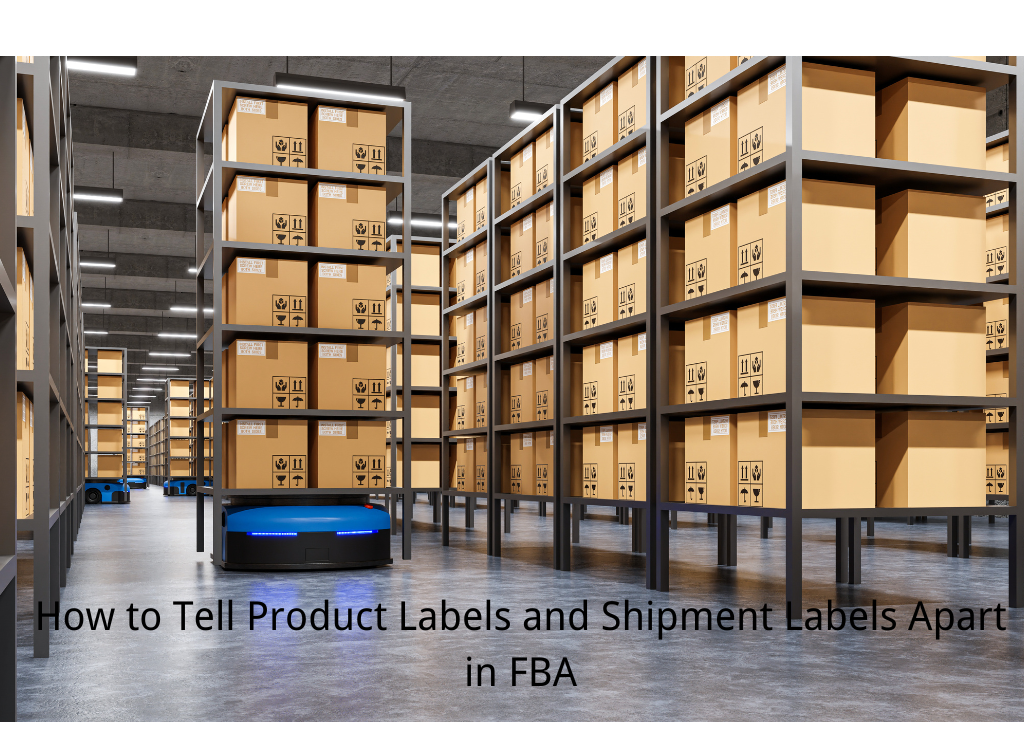
Shipping oversized items to Amazon FBA isn’t as straightforward as just packing your goods and sending them off.Whether you’re handling your own shipments or working with a China freight forwarder, there are rules and regulations you absolutely need to follow to avoid costly mistakes.Imagine this: You ship a 120-pound couch without the right labels or packaging, and it gets rejected at the FBA warehouse.Or, even worse, you end up paying hefty fees for non-compliance. This isn’t just a hassle – it’s a drain on your profits.That’s why it’s crucial to know the ins and outs of oversized shipping before you even pack your boxes. Let’s dive into the essential tips for making sure your oversized items make it to Amazon’s FBA warehouse without any issues.Understand Amazon’s Size and Weight RulesAmazon loves rules, and oversized items have their own playbook. Mess this up, and your shipment could get rejected, cost more, or take forever to check in. Here’s what you need to know:Size LimitsStandard-sized boxes: Any side can’t exceed 64 centimeters.Oversized items: Must ship in individual boxes – no bundling multiple oversized products together.Packaging after assembly: If your item is already pushing size limits, make sure the packaging doesn’t tip it over Amazon’s maximum size requirements.Weight RegulationsItems over 100 lbs (45 kg): Add a “Mech Lift” label so everyone knows a machine is required.Items 50–100 lbs (22.5–45 kg): Use a “Team Lift” label to indicate team handling.Jewelry and watches: Keep the box weight under 40 lbs (18 kg). Yeah, they’re picky like that.Nail the Packaging – No Room for ErrorsPackaging isn’t just about looking professional – it’s about surviving the journey.Here’s How to Pack Like a Pro:Use six-sided hard boxes – no floppy cardboard that crumbles under pressure.Clear old labels before slapping on new ones. Trust me, mixed-up barcodes are a nightmare.Add Amazon-specific labels on every box – these are non-negotiable.For bulk shipments? Label both the outer big box and every inner box.Bonus Tip:Fill empty spaces with high-quality padding to prevent internal movement. Shipping is like bumper cars – your items will take a hit, but good padding keeps them intact.Pre-Label and Prep Like It’s Your Job (Because It Is)Amazon’s system relies on labels. Without proper prep, your inventory could disappear into the void.Individual item packaging: Use bubble wrap, foam, or whatever it takes to keep your products secure.Right-sized boxes: Avoid oversized boxes with too much empty space – they’re more prone to damage.Unique labels: Every item and box needs its own unique label to avoid mix-ups.If You’re Using Pallets, Do It RightPallets aren’t just for giant warehouses. They’re your best friend for heavy-duty shipping. But Amazon’s picky about this too:Pre-schedule your pallet delivery. Show up unannounced? That’s a quick way to get turned away.Make sure your pallets meet Amazon’s size and material standards.Label both pallets and individual boxes.Cost Control – Don’t Bleed MoneyShipping oversized items is already pricey, but you can still control your costs. Here’s how:Dimensional weight pricing: Carriers charge by size AND weight. Pack efficiently to avoid paying for wasted space.Use freight forwarders that specialize in FBA to save on international shipments.Try using Amazon’s partnered carrier programs for bulk discounts.Avoid Rookie MistakesDon’t learn the hard way. Here are the most common mistakes sellers make – and how to avoid them:Ignoring weight and size rules: Even 1 cm over the limit could trigger extra fees or rejection.Old labels: Forgetting to clear them leads to massive delays.Insecure packaging: Fragile items WILL get damaged if not properly packed.Always Follow Amazon’s Rules – No ShortcutsAmazon doesn’t mess around. If you cut corners, expect rejected inventory, hefty fees, or worse – your account suspended.Follow their rules for:Safety requirementsLabeling and prepSpecific product restrictionsLet’s Make This RealImagine this: You ship a 120 lb couch to Amazon without a “Mech Lift” label. It arrives damaged, gets flagged as unsafe, and you’re charged return fees. Ouch, right?Now imagine you followed the rules. Same couch arrives intact, Amazon stocks it seamlessly, and you start making money. The choice is obvious.FAQsCan I bundle multiple oversized items in one box?Nope. Amazon requires oversized items to ship individually.What’s the most cost-effective way to ship oversized items?Use freight forwarders or Amazon’s partnered carrier programs. These can save you money, especially for international shipments.What happens if my shipment doesn’t meet Amazon’s requirements?Your items could be rejected, returned, or even destroyed – and you’ll foot the bill.Final WordsShipping oversized items to Amazon FBA isn’t rocket science, but it does take some effort.Get the size and weight right. Nail the packaging. Follow Amazon’s rules like your business depends on it – because it does.Start small, test your process, and keep optimizing.Shipping smarter means happier customers, smoother operations, and more money in your pocket.And who doesn’t want that?
2024-12-03
11
Amazon FBA
Overseas Warehouses
Sea Freight
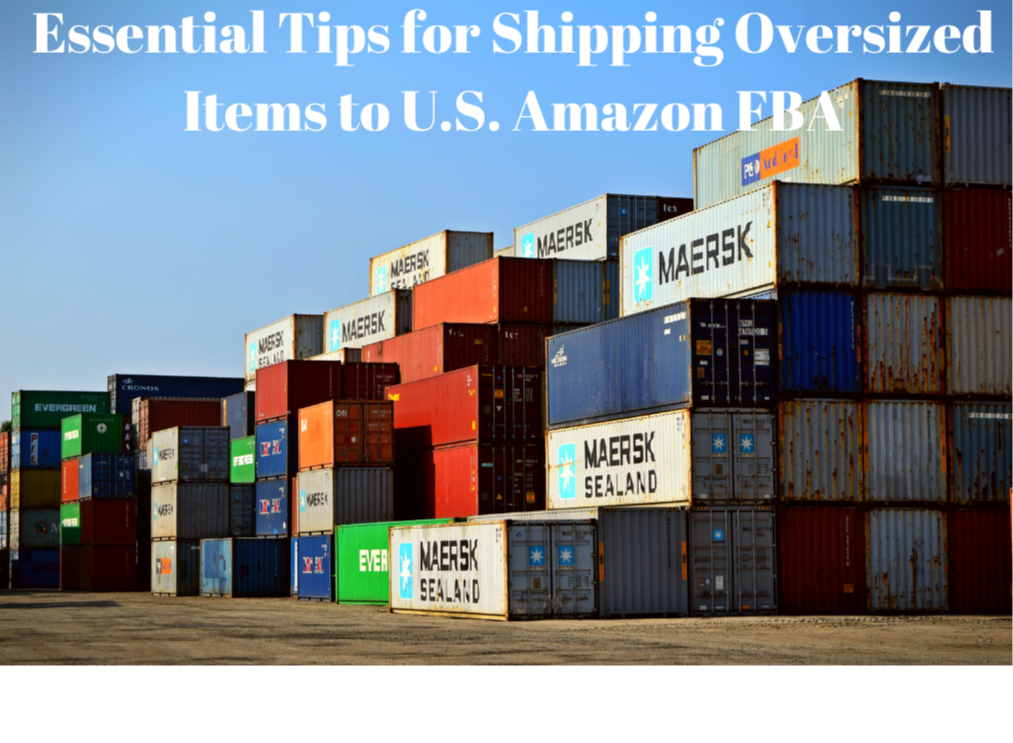
When preparing for FBA (Fulfilled by Amazon) full container loading, it's crucial to follow these key steps to ensure the safety of your goods and smooth delivery to Amazon warehouses. By adhering to these guidelines, you can minimize risks, streamline the process, and ensure compliance with Amazon’s requirements.1. Product PackagingProper packaging is the foundation of safe and efficient transport.Use Durable Cartons:Ensure products are packed in sturdy corrugated cartons that can withstand the rigors of transit. Reinforce the interior with custom foam or padding to prevent deformation or damage during shipping.Check for Damage:Inspect all packaging for rips, tears, or other damage. Amazon often rejects goods with damaged or deformed packaging.Seal Securely:Use strong packing tape to seal cartons, avoiding any chance of accidental opening during transit.2. Correct LabelingAccurate labeling is essential for Amazon to process your shipment smoothly.FBA Labels:Ensure every product and carton has the correct FBA label, which must be scannable and free of smudges or scratches.Special Handling Labels:For cartons weighing over 50 pounds, apply a "Team Lift" label.For those exceeding 100 pounds, use a "MechLift" label.These labels are mandatory for compliance with Amazon’s handling requirements.Placement Tips:Avoid placing labels on carton seams or edges. They should be on a flat surface, fully visible.3. Compliance with Size and Weight LimitsAdhering to Amazon’s size and weight restrictions reduces the risk of delays or rejections.Weight Limits:No single carton should weigh over 50 pounds unless explicitly allowed for specific products or warehouse policies. Always verify weight regulations for your designated fulfillment center.Volume Restrictions:Ensure that cartons are not excessively large, as oversized boxes can create handling challenges and attract additional fees.Mark Oversized Cartons:If a carton exceeds standard dimensions or weight, clearly mark it as oversized to alert handlers and prevent mismanagement.4. Efficient Loading TechniquesProper loading techniques are critical to protecting your goods during transport and ensuring efficient unloading at the warehouse.Avoid Overloading or Underloading:Load cartons with balanced spacing. Avoid packing too tightly or too loosely to minimize movement during transit.Stair-Step Pattern Near Doors:Arrange the last two rows in a stair-step pattern. This configuration facilitates smoother unloading at Amazon’s docks.Leave Space at the Top:Maintain at least 8 inches (20 cm) of clearance at the top of the container to avoid issues with overhead beams or forklift access.Carton Gaps:Leave at least 3 inches (7.6 cm) between cartons to prevent them from getting stuck during handling.5. Implement Safety MeasuresTo prevent damage or shifting during transit, secure your shipment thoroughly.Space Between Last Row and Door:Leave a buffer zone of at least 8 inches (20 cm) between the last row of cartons and the container doors.Stabilizing Equipment:Use tools like dunnage bags, non-metal strapping, bracing rods, or safety nets to secure the cargo and prevent it from shifting. Avoid using sharp materials that might damage cartons.6. Prepare Necessary DocumentationBefore shipping, ensure that all required documents are completed and accurate.Customs Clearance Documents:Include detailed product descriptions, invoices, and any other paperwork necessary for customs processing.FBA Shipment Plan:Confirm that the shipment is accurately documented in your Amazon Seller Central account to avoid discrepancies.Backup Copies:Keep digital and physical copies of all shipping documents in case of emergencies.7. Understand FBA FeesHaving a clear understanding of FBA fees helps you budget effectively and avoid surprises.Storage Fees:Amazon charges storage fees based on the time your goods stay in their warehouse. Familiarize yourself with both standard and peak-season rates.Handling Costs:Oversized, heavy, or non-compliant shipments may incur extra handling charges.8. Insurance and Inventory MonitoringProtecting your shipment and tracking its journey are vital for peace of mind.Shipping Insurance:Purchase transportation insurance to cover any potential loss or damage during transit.Real-Time Monitoring:Use inventory tracking tools to monitor the shipment status and confirm its safe arrival at the designated FBA warehouse.Additional Tips for SuccessPartner with a reliable freight forwarder experienced in FBA shipments.Conduct a final inspection of the container before sealing it for transit.Maintain open communication with your logistics provider to address any last-minute issues.By following these steps, you can significantly reduce risks and streamline the process of delivering your FBA shipments to Amazon’s warehouses. Proper planning and meticulous execution will not only ensure compliance but also enhance your operational efficiency.FAQsWhat is the maximum weight allowed for FBA cartons?The maximum weight for FBA cartons is typically 50 pounds unless otherwise specified by Amazon.Why should I leave space at the top of the container?Leaving 8 inches of space helps prevent handling issues and ensures compliance with Amazon’s unloading procedures.What safety measures can prevent cargo shifting?Use dunnage bags, straps, or safety nets to secure goods and maintain stability during transit.
2024-11-26
20
Amazon FBA
Overseas Warehouses
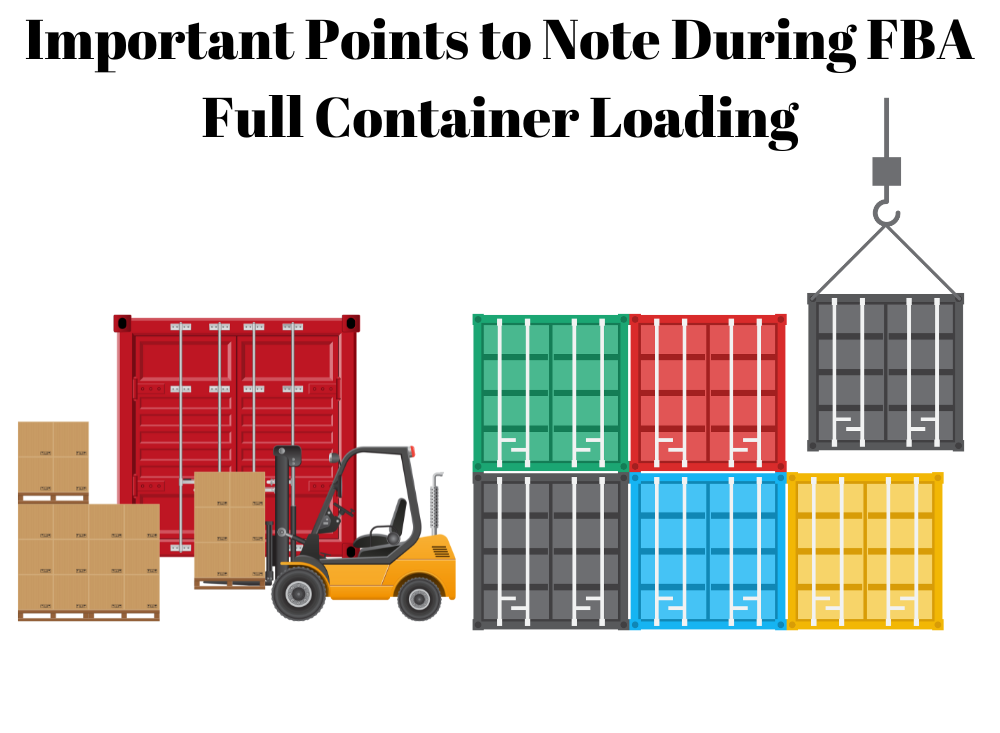
Efficient inventory replenishment is crucial for Amazon FBA (Fulfillment by Amazon) sellers to prevent stockouts, reduce storage costs, and optimize cash flow. This guide breaks down key strategies and processes tailored to different product lifecycle stages, ensuring you stay ahead in managing your FBA inventory.1. Replenishment Strategy for New ProductsNew products require careful planning to ensure adequate stock while minimizing overstock risks.Sales ForecastingUse metrics like review rate and average reviews to estimate future sales.Calculation formula:Reorder Quantity = (Lead Time + FBA Inbound Time + Inventory Receiving Time) × 30-Day Average Daily Sales – In-Transit Inventory – Current InventoryExampleDaily sales: 30 unitsLead time: 10 daysFBA inbound and receiving time: 25 daysIn-transit inventory: 300 unitsCurrent inventory: 450 unitsRequired Order = (10 + 25) × 30 – 300 – 450 = 300 units2. Replenishment Strategy for Growth StageDuring the growth stage, it is essential to maintain consistent inventory levels to support increasing sales while accounting for market fluctuations.Average Sales MonitoringMaintain at least one month's inventory on hand.Regularly review sales trends and adjust forecasts to avoid overestimating demand.3. Replenishment Strategy for Maturity StageIn the maturity stage, the focus shifts to balancing inventory levels to minimize storage costs while preventing stockouts.Cost Control with "Just-in-Time" ShippingImplement a "small but frequent" replenishment approach.Ship weekly using sea freight, aligning shipment quantities with one week’s sales volume.Aim to keep FBA inventory levels above 50 days of supply.4. Replenishment WorkflowInventory Data ManagementDownload Inventory and Sales Reports:Pull data from Amazon's backend, though this can be time-intensive with a large number of SKUs.Leverage ERP Systems (e.g., WIMOOR ERP):Automating calculations and streamlining processes saves time and improves accuracy.Key Features of ERP Systems:Inventory and Order Management: Seamlessly track and manage products, purchase orders, and storage.Smart Procurement: Automatically calculate replenishment needs for multiple stores and marketplaces.Shipping Optimization: Plan shipments to prevent stockouts and reduce warehousing fees.Real-Time Inventory Monitoring: Minimize excess storage costs while improving cash flow.5. Steps to Create an FBA ShipmentUpload Product Information: Choose the FBA fulfillment option in your Amazon seller account.Select Amazon Barcode: Convert to Amazon-standard barcodes for inventory.Provide Dangerous Goods Information: Fill in hazard details if applicable.Set Shipping Address and Packaging Details: Define your shipment destination and packing type.Create Shipment and Input Packing Information: Include quantities, weights, and dimensions.Print and Attach Labels: Ensure boxes are labeled correctly before shipping.6. Advantages of Using ERP ToolsERP systems enhance the replenishment process by automating and simplifying complex workflows.Benefits:Automation: Sync directly with Amazon’s backend, eliminating the need for frequent manual logins.Dynamic Calculations: Auto-generate replenishment suggestions based on real-time sales data.Open Source and Scalability: Systems like WIMOOR ERP offer open-source versions, enabling modular upgrades and commercial use.ConclusionBy following these steps and leveraging the strategies outlined above, Amazon sellers can streamline their FBA inventory replenishment process, minimize risks of stockouts, control storage costs, and optimize cash flow. Whether you’re managing new products, navigating growth stages, or optimizing mature SKUs, an effective inventory strategy ensures long-term success on the Amazon platform.FAQsHow can I calculate the right amount of inventory to reorder?Use this formula: (Lead Time + FBA Inbound Time + Receiving Time) × Daily Sales – In-Transit – Current Inventory.What is the best way to handle inventory during peak sales periods?Use an ERP system to monitor real-time sales and automate replenishment suggestions for seamless restocking.How do ERP tools help with FBA inventory management?ERP tools automate calculations, optimize shipments, reduce storage costs, and ensure inventory balance.
2024-11-22
15
Amazon FBA
Overseas Warehouses
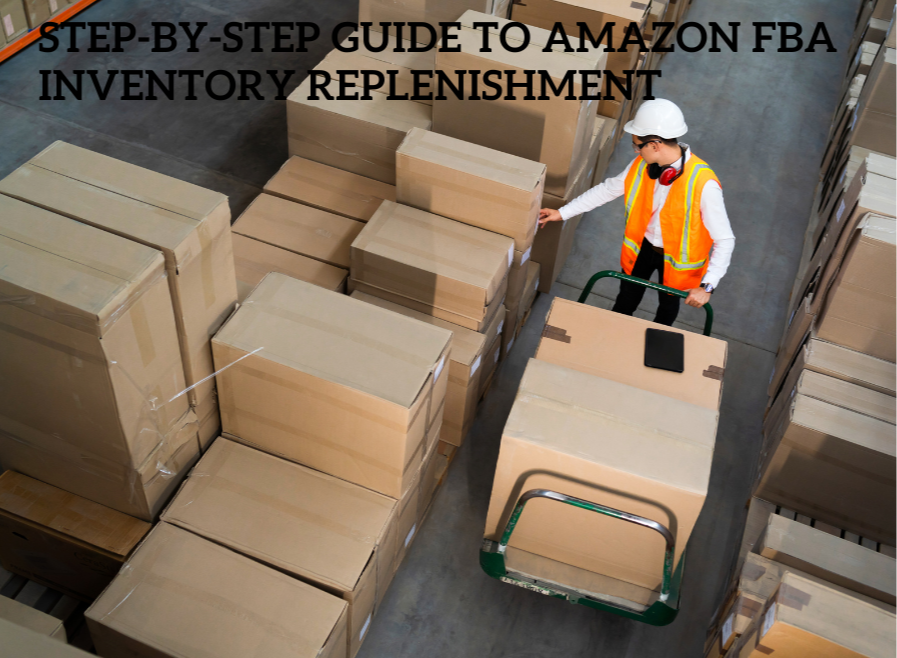
Hey there, fellow Amazon sellers! If you're diving into the world of FBA (Fulfillment by Amazon), you've probably realized that getting your products into Amazon's warehouses isn't as simple as just boxing them up and shipping them off. Trust me, I've been there, and I know how overwhelming those pallet requirements can seem at first. If you're working with a freight forwarder China to US, you’ll need to make sure everything is set up correctly to avoid any delays. But don’t worry – I'm here to break down everything you need to know about Amazon FBA pallet standards in a way that actually makes sense.Why Proper Pallet Preparation MattersBefore we dive into the nitty-gritty details, let's talk about why this stuff really matters. Picture this: your products arrive at Amazon's warehouse, but they're not properly palletized. Best case scenario? Delays. Worst case? Rejected shipments and a hefty bill. I've seen sellers lose thousands of dollars simply because they didn't understand these requirements. But that's not going to be you – because we're going to get this right from the start.The Real Cost of Non-ComplianceYou might be thinking, "Come on, how big a deal can pallet requirements really be?" Well, here's the truth: Amazon processes millions of items daily, and they've optimized their warehouses down to the smallest detail. When you don't follow their guidelines, you're essentially throwing a wrench in their well-oiled machine. This can lead to:Additional processing fees (sometimes up to $200 per pallet!)Shipping delays of 1-2 weeksPotential inventory stockoutsAccount performance metrics taking a hitGetting Your Pallet Basics RightLet's start with the foundation – literally! The right pallet can make or break your FBA journey.Choosing the Perfect PalletEver tried wearing shoes that don't fit? That's what using the wrong pallet size is like for Amazon's warehouses. Here's what you need to know by region:North America, Australia, Middle East, UK, India, Singapore: Go for 120 cm x 100 cmEurope (excluding UK): Stick to 120 cm x 80 cm EPAL/EUR palletsJapan: You'll need 110 cm x 110 cmPro tip: Those EPAL/EUR pallets need special markings on both sides – don't forget to check for them!Material MattersYou can't just use any old pallet you find behind your local grocery store. Amazon has specific requirements:Wood pallets must be heat-treated or fumigated (look for the ISPM15 stamp)No broken boards or protruding nails (that's just asking for trouble)Clean and dry (moisture is your inventory's enemy)Mastering the Art of StackingNow that we've got our pallet situation sorted, let's talk about how to stack your products like a pro.Height and Weight Guidelines That Actually Make SenseI know it's tempting to stack your products as high as possible to save on shipping, but here's what you really need to know:Height Limits:US & UK: Keep it under 180 cm (that's about 5'11")Germany, France, Italy, Spain: Max 170 cmJapan: Has its own specific requirements (always check the latest guidelines)Weight Limits:Generally: Stay under 500 kg total (including pallet weight)Japan: Can go up to 1000 kg (they're generous like that!)The Art of Safe StackingHere's something they don't always tell you: how you stack matters just as much as how high you stack. Follow these tips:Start with heavier items at the bottom (seems obvious, but you'd be surprised!)Keep boxes aligned (no Jenga-style arrangements)Use corner supports for extra stabilityLeave no gaps between boxes (they're like cavities in your pallet's smile)Packaging and Labeling: The Make-or-Break DetailsThis is where many sellers stumble, but I've got you covered.Creating Label-Perfect PalletsEvery box needs:FNSKU labels (think of these as your product's social security number)Shipping labels (your package's passport)Special handling labels when neededAnd here's a golden tip: Place pallet labels on ALL FOUR SIDES. Why? Because warehouse workers aren't going to play Twister trying to find your labels!The Wrap GameThink of stretch wrap as your pallet's seatbelt. Here's how to do it right:Use clear, sturdy stretch wrapStart from the bottomOverlap each layer by 50%Go up and down at least twiceNo ropes or straps (Amazon hates those)Special Situations and Smart SolutionsWhen Standard Just Won't Cut ItGot oversized items? Products that don't fit the mold? Here's what to do:Contact Amazon support BEFORE shippingRequest special handling instructionsBe prepared with alternative solutionsDocument everything (seriously, everything)Eco-Friendly Packaging OptionsLet's face it – customers care about sustainability now more than ever. Here's how to go green:Use recycled materials when possibleOpt for minimal packagingChoose biodegradable options where availableSkip the fancy marketing inserts (Amazon doesn't want them anyway)Final Tips for FBA SuccessCommunication is KeyKeep Amazon in the loop about special requirementsDocument all communicationsTake photos of your packed pallets (trust me, these can save you later)Stay updated on policy changesCommon Mistakes to AvoidLearn from others' mistakes (so you don't have to make them yourself):Not checking regional requirementsSkimping on wrapping materialsForgetting to label all sidesMixing different SKUs without proper separationReady to Ship? Your Final ChecklistBefore you send that pallet on its way, run through this quick checklist:Correct pallet size for your region? ✓Products properly stacked and secured? ✓All required labels in place? ✓Weight and height within limits? ✓Stretch wrap properly applied? ✓Special handling requirements addressed? ✓Remember, success in Amazon FBA isn't just about having great products – it's about getting those products into Amazon's warehouses smoothly and efficiently. By following these guidelines, you're setting yourself up for successful fulfillment and happy customers.Want to learn more about Amazon FBA success strategies? Drop a comment below or check out our other guides on inventory management and FBA optimization!
2024-11-12
9
Amazon FBA
Overseas Warehouses
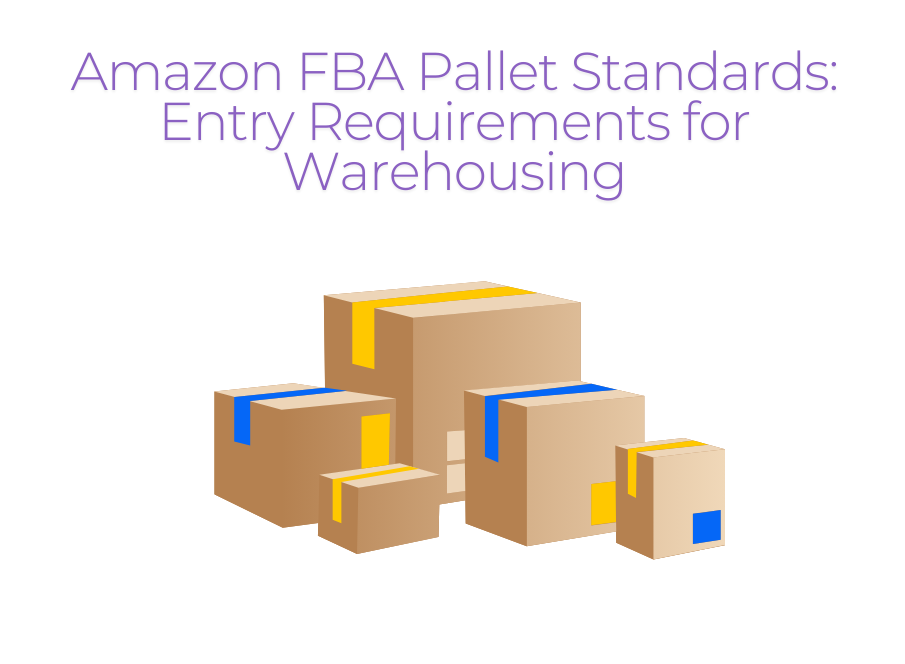
When considering logistics solutions for cross-border e-commerce, choosing between Fulfillment by Amazon (FBA) and third-party overseas warehouses is crucial.Sellers shipping products internationally, such as using a freight forwarder china to usa, often face decisions that impact everything from cost to delivery speed.This makes it essential to understand which option suits your business best.Quick OverviewFBA: Amazon's integrated fulfillment serviceOverseas Warehouses: Independent logistics solutions with customizable servicesService Provider ComparisonAmazon FBAManagement: Directly operated by AmazonIntegration: Seamless integration with Amazon's marketplaceCoverage: Global fulfillment networkProcess: Centralized handling of storage, picking, packing, and shippingQuality Control: Standardized Amazon proceduresScalability: Easily scalable during peak seasonsThird-Party Overseas WarehousesManagement: Independent logistics providersIntegration: Compatible with multiple sales channelsCoverage: Varies by providerProcess: Customizable operationsQuality Control: Varies by providerScalability: Dependent on warehouse capacityProduct Compatibility and RestrictionsFBA RequirementsSize Limitations: Strict size and weight restrictionsProduct Categories: Some restrictions on hazardous materialsBest Suited For:Small to medium-sized itemsHigh-turnover productsPremium-priced itemsLightweight merchandiseOverseas Warehouse FlexibilitySize Limitations: More flexibleProduct Categories: Broader acceptanceBest Suited For:Large itemsHeavy productsSpecialized equipmentSeasonal merchandiseBulk inventoryLogistics and TransportationFBA LogisticsFirst-Mile Transport: Not includedCustoms Clearance: Seller's responsibilityLast-Mile Delivery: Managed by AmazonDelivery Speed: Prime-eligible fast shippingGeographic Coverage: Amazon's established marketsOverseas Warehouse LogisticsFirst-Mile Transport: Often includedCustoms Clearance: Usually handled by providerLast-Mile Delivery: Multiple carrier optionsDelivery Speed: Varies by location and carrierGeographic Coverage: More flexible, including emerging marketsCost Structure AnalysisFBA CostsFixed CostsStorage Fees: Monthly rates vary by seasonFulfillment Fees: Based on size/weightLong-term Storage: Penalties after 365 daysReturn Processing: Additional fees applyVariable CostsPeak Season Surcharges: Higher rates during Q4Removal Orders: Fees for inventory removalMulti-Channel Fulfillment: Extra fees for non-Amazon ordersOverseas Warehouse CostsFixed CostsStorage Fees: Usually lower than FBAHandling Fees: Often negotiableProcessing Fees: Based on service levelVariable CostsVolume Discounts: Available for larger quantitiesCustom Services: Additional fees for special handlingReturn Processing: Typically more flexible pricingInventory ManagementFBA Inventory ControlDistribution: Amazon controls inventory placementTracking: Real-time inventory visibilityRestock Limits: Subject to Amazon's restrictionsStorage Limits: Based on IPI scoreCommingling: Possible with identical productsOverseas Warehouse ControlDistribution: Seller controls inventory placementTracking: Provider-dependent systemsRestock Limits: More flexibleStorage Limits: NegotiableCommingling: Usually not practicedMarketing and Sales ImpactFBA BenefitsPrime Badge: Enhanced visibilityBuy Box Advantage: Higher win rateCustomer Trust: Amazon's reputationSearch Ranking: Potential algorithm advantagePromotional Eligibility: Access to Amazon dealsOverseas Warehouse ConsiderationsPlatform Independence: Multi-channel sellingPricing Flexibility: Lower overhead costsBrand Control: Better brand identity managementCustom Packaging: Available optionsPromotional Freedom: Unrestricted by Amazon rulesCustomer Service and ReturnsFBA Customer ServiceSupport: Handled by AmazonReturn Process: StandardizedResolution Time: Usually quickQuality Consistency: High standardsLanguage Support: Multiple languagesOverseas Warehouse SupportSupport: Seller-managed or provider-managedReturn Process: CustomizableResolution Time: Varies by providerQuality Consistency: Depends on providerLanguage Support: Varies by locationRisk ManagementFBA RisksAccount Suspension: Inventory access affectedCompetition: Nearby similar productsCost Fluctuations: Subject to Amazon's changesStorage Limitations: Seasonal restrictionsPlatform Dependency: Amazon-centricOverseas Warehouse RisksProvider Stability: Varies by companyService Quality: Less standardizedCommunication: Potential language barriersIntegration Issues: Technical challengesMarket Coverage: May require multiple providersBusiness ScenariosBest for FBAHigh-volume Amazon sellersPrime-focused businessesSmall, lightweight productsFast-moving inventoryBrand registry sellersBest for Overseas WarehousesMulti-channel sellersLarge or heavy productsCustom handling requirementsSlow-moving inventoryBudget-conscious operationsMaking Your DecisionConsider These FactorsBusiness Model: Your sales channels and strategyProduct Characteristics: Size, weight, and special requirementsBudget: Initial and ongoing costsControl Needs: Inventory and fulfillment flexibilityMarket Focus: Geographic targets and customer baseGrowth Plans: Scalability requirementsService Level: Customer experience prioritiesAction StepsAnalyze Your Products: Review your catalogCalculate Costs: Compare total expensesAssess Markets: Evaluate target regionsReview Requirements: Check compliance needsTest Options: Start with pilot programsConclusionBoth FBA and overseas warehouses offer distinct advantages for cross-border e-commerce. FBA provides a streamlined, trusted solution ideal for Amazon-focused sellers, while overseas warehouses offer flexibility and customization for diverse business needs. Many successful sellers use a hybrid approach, leveraging both options for different products or markets.Additional ResourcesAmazon FBA GuidelinesLogistics Provider DirectoriesCost Calculation ToolsCompliance ChecklistsMarket Analysis ReportsRemember that the best choice depends on your specific business needs, and these solutions can be used complementarily to optimize your global e-commerce operations.
2024-11-08
19
Overseas Warehouses
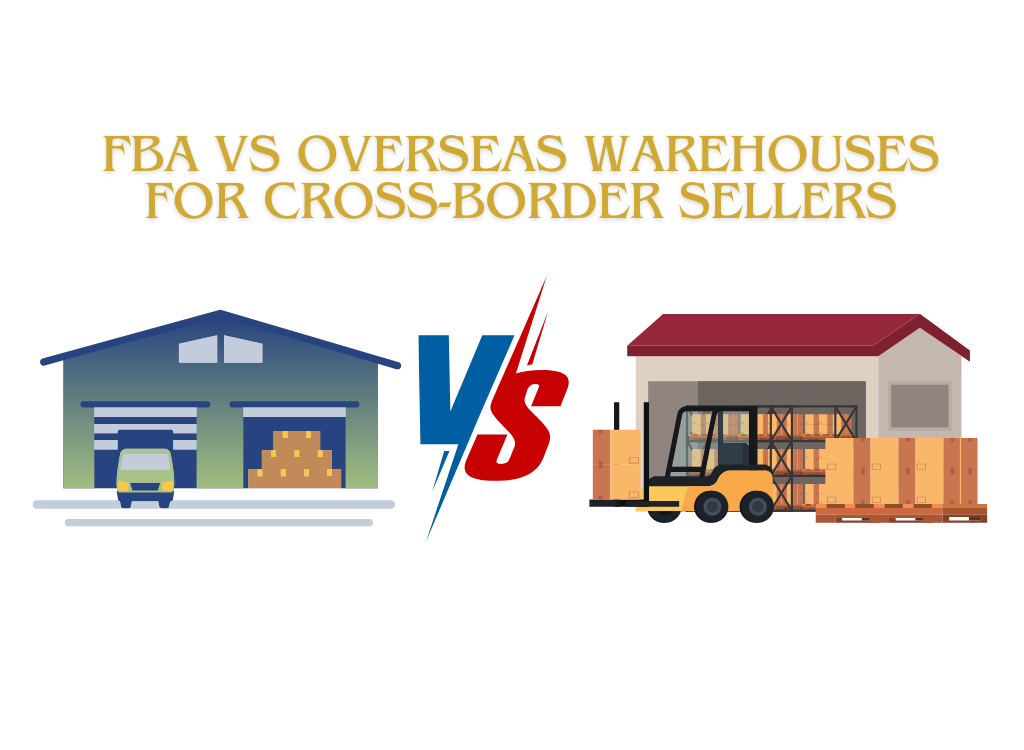
Are you struggling to choose the perfect overseas warehouse for your e-commerce business?You're not alone. Whether you're working with a China freight forwarder or managing logistics on your own, finding the right fit can feel overwhelming. Let's break down everything you need to know to make the best choice for your business.Understanding Different Warehouse Types (And Why It Matters)Selecting the right type of warehouse is like choosing a business partner - it needs to match your operational style, budget, and growth plans.Each warehouse type comes with its own unique advantages and trade-offs. Let's explore your options and find out which one aligns best with your business goals.E-commerce Platform Warehouses (Like Amazon FBA)Ever wondered why some sellers seem to dominate marketplace rankings? Platform warehouses might be their secret weapon. Here's what you get:✨ Built-in Platform Integration: Your products get processed and shipped lightning-fast📈 Better Visibility: Think higher search rankings and more "recommended" placements🎯 Prime Eligibility: Tap into millions of Prime subscribersReal-world example: A small electronics seller saw their sales jump 40% in their first month after switching to Amazon FBA, mainly due to Prime badge visibility.Self-Operated Warehouses: Taking ControlThink of this as having your own overseas business headquarters. Is it right for you?🎛️ Complete Control: Design your storage layout? Check. Set your own rules? Double-check.💰 Long-term Savings: Higher upfront costs, but potentially better margins over time⚠️ Management Challenge: You're the captain of this ship - exciting but demandingThird-Party Warehouses: The Flexible FriendNeed a balance between control and convenience? Third-party warehouses might be your sweet spot:🔄 Multi-Platform Support: Sell everywhere without the headache📦 Comprehensive Services: From customs clearance to quality checks💪 Scalability: Grow or shrink your storage needs as neededPublic Warehouses: Sharing Is Caring (And Saving)Perfect for smaller businesses or those testing new markets:👥 Cost Sharing: Split expenses with other businesses🏃♂️ Quick Start: No major investment needed📏 Standard Processes: Less flexibility, but proven systemsBonded Warehouses: The Cash Flow ChampionDid you know you can delay import duties until you actually sell your products?💵 Better Cash Flow: Pay duties only when products leave the warehouse📋 Strict Compliance: Heavy regulation, but worth it for the right business🎯 Ideal for: High-value goods or bulk importsService Types: Finding Your Perfect MatchNow that we understand the different warehouse types, let's dive into the various service models available.The right service type can dramatically impact your operational efficiency and customer satisfaction. Think of these services as different tools in your logistics toolkit - each designed for specific business scenarios.Full-Service WarriorsThese warehouses do it all:🎯 One-Stop Solution: Storage, fulfillment, returns - you name it⚡ Quick Market Response: Perfect for fast-moving consumer goods💪 Value Add: Some even handle product customization and packagingDrop-Shipping SpecialistsRunning a lean operation? This might be your answer:🚀 Speed Demons: Specialized in quick, single-item fulfillment💰 Cost-Effective: Bulk shipping rates for individual orders📦 No Inventory Headaches: Perfect for testing new productsTransit ProsThink of these as your logistics pit stop:🔄 Quick Turnaround: Minimal storage, maximum movement🌐 Network Power: Great for complex international shipping routesCross-Docking ChampionsWhen speed is everything:⚡ Ultra-Fast Processing: Items barely touch the ground🚛 Seamless Integration: Perfect for time-sensitive deliveriesAfter-Sales HeroesBecause the sale isn't the end of the story:🛠️ Full Support: Returns, repairs, and refurbishment💎 Perfect for: High-value items needing warranty serviceMaking Your Choice: Key Questions to AskBefore you decide, ask yourself:What's my monthly shipping volume?How fast do my customers expect delivery?What's my budget for warehousing?Do I need special handling for my products?Which markets am I targeting?Pro Tips for Success🎯 Start small with a flexible provider📊 Track performance metrics religiously🤝 Build relationships with multiple providers📈 Regular review and optimization is keyRemember: The right warehouse partner can make or break your cross-border e-commerce success. Take your time, do your research, and choose a solution that can grow with your business.
2024-11-08
11
Overseas Warehouses
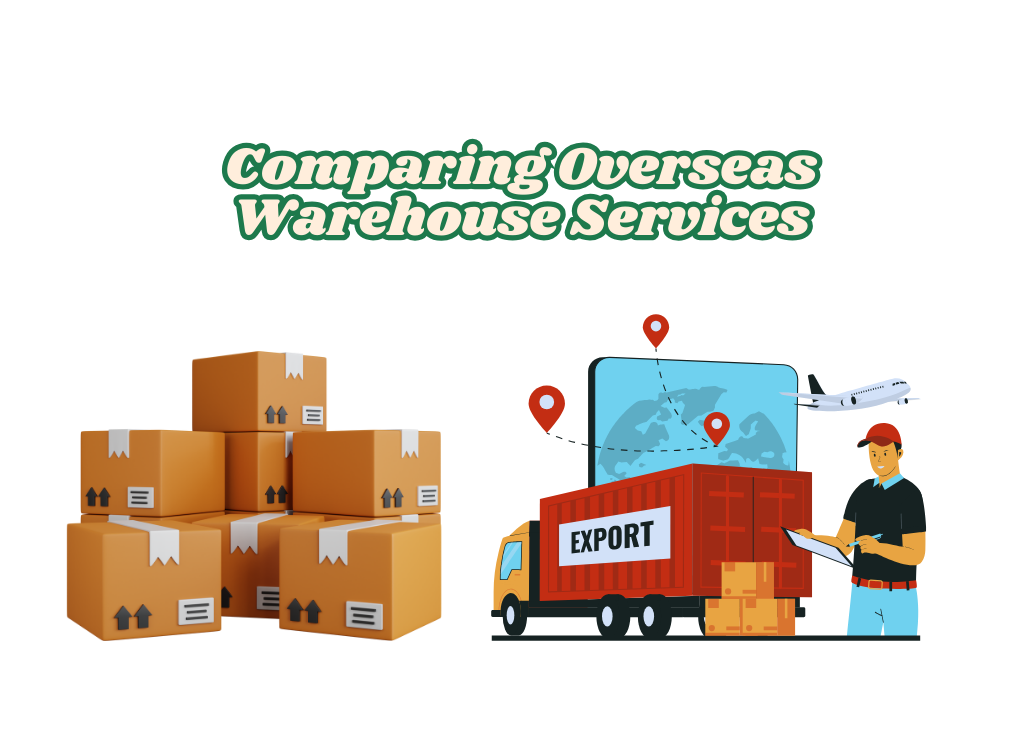
Amazon FBA (Fulfillment by Amazon) warehousing time may vary depending on a variety of factors, including warehouse operations, the type and quantity of goods, transportation methods, and whether it is in peak season.Amazon FBA warehousing time1. Warehousing time concept: Amazon FBA warehousing time refers to the time Amazon receives, registers, classifies and puts on the shelves after the seller delivers the product to the Amazon warehouse.2. Factors affecting warehousing time: The warehousing time is affected by a variety of factors, including product characteristics, warehouse location, logistics timeliness, order processing speed, etc.3. Warehousing time range: Generally, Amazon FBA warehousing time is completed within 2-5 working days. However, the specific time needs to be evaluated based on the seller's product characteristics and warehouse requirements.Amazon FBA Warehousing Requirements1. Product requirements:a. Comply with Amazon sales policies and regulations, such as not containing banned, restricted or infringing products;b. Product quality meets standards, no damaged, missing or defective products;c. Product labels are correct, clear and consistent, including UPC codes, SKU codes, etc.2. Packaging requirements:a. Comply with Amazon's packaging requirements, such as using boxes of appropriate size, shockproof materials, etc.;b. Ensure that the product is not damaged during transportation, especially fragile or sensitive products;c. Attach necessary labels, such as shipper information, product name, quantity, etc.3. Document requirements:a. Provide an accurate product list or invoice, including product name, quantity, price, etc.;b. Provide necessary import documents and certificates (such as tariff and tax certificates, etc.);c. Provide product certification documents or authorization letters (such as CE certification, RoHS certification, etc.).4. Other requirements:a. Comply with Amazon's transportation and warehousing regulations, such as following shipment restrictions, overweight restrictions, etc.b. Ensure that shipments are delivered to Amazon warehouses safely and in an orderly manner to avoid delays and losses;c. Work with Amazon to solve problems and provide necessary support.Here are Some Factors that Affect the Warehousing Time:1. Transportation time: The transportation time from the place of shipment to the Amazon warehouse is one of the main factors affecting the warehousing time.2. Warehouse receiving capacity: The receiving and processing capacity of Amazon warehouses will also affect the warehousing speed. During peak periods, such as holiday shopping seasons, warehouses may be busier, resulting in longer warehousing time.3. Type of goods: Different types of goods may require different processing times. For example, perishables, dangerous goods, or goods that require special handling may require more time.4. Quantity of goods: It may take longer to enter the warehouse for a large number of goods because Amazon needs more time to process and store them.5. Appointment delivery: Amazon requires sellers to make an appointment for the delivery of goods. Failure to deliver on time may affect the warehousing time.6. Goods preparation: If the goods are not properly packaged and labeled as required by Amazon, it may cause warehousing delays.7. Customs clearance process: For international shipments, the customs clearance process may also affect the time it takes for goods to arrive at Amazon warehouses.Generally, Amazon recommends that sellers plan ahead and take into account all possible delay factors. Some sellers report that during off-peak periods, it may take a few days to a week for goods to be delivered to Amazon warehouses and put on the shelves. However, this time may vary depending on the above factors.To reduce warehousing time, sellers can take the following measures:Ensure that the packaging and labeling of goods meet Amazon's requirements.Make an appointment for the delivery of goods in a timely manner and try to keep the appointment.Consider using a logistics service provider recommended by Amazon.Track the shipping status of the goods so that you can take timely action if there are delays.If you need a more accurate estimate of the warehousing time, it is recommended to contact Amazon Seller Support directly or use the resources of Amazon Seller Center
2024-05-29
22
Overseas Warehouses
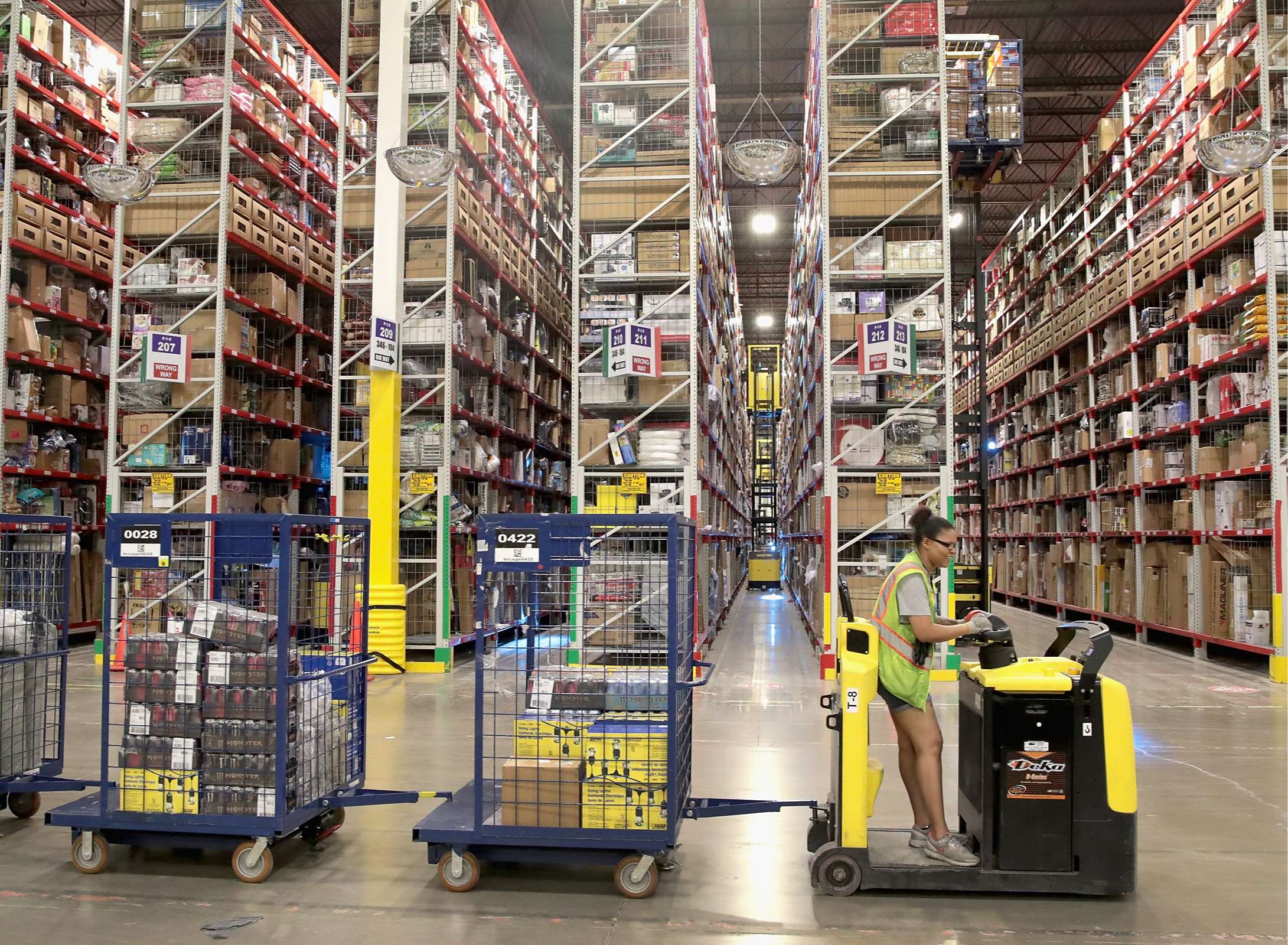